闭口槽铸铝转子对西玛电机电机性能的影响。
时间:2019-08-18 13:24
Ms参陪朋友小H到一家
电机厂考察,顺便看看他订购的一批YE3高效
电机进展状况如何。在机加工段转子车气隙现场,小H提出质疑:为何有的转子精车后是一道一道的,而有的则是一个整体的光面?现场工人回应了一句,看不见道的是高效电机。小H表情亮了,向Ms.参问了些高效电机方面的相关知识,了解到整体光面的转子乃为闭口槽的缘故,一道一道的是槽口。
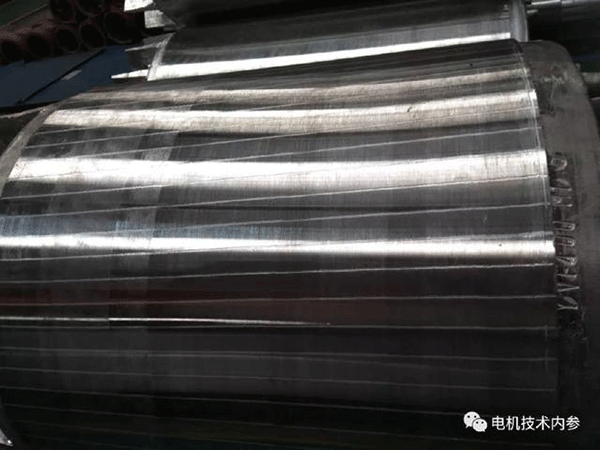
为何高效电机要用闭口槽?
普通笼型异步电动机的鼠笼转子一般采用半闭口槽,这里高效电机应用闭口槽,有两方面的考虑:一是降低了气隙磁阻,激磁电流相对来讲要小一些,产生的铜损耗也小;二是可以有效减少电机因磁导谐波在铁芯表面脉振产生的附加铁芯损耗。显然,双重因素的效率提升作用颇具杀伤力,故而各厂家纷纷大面积试用转子闭口槽。
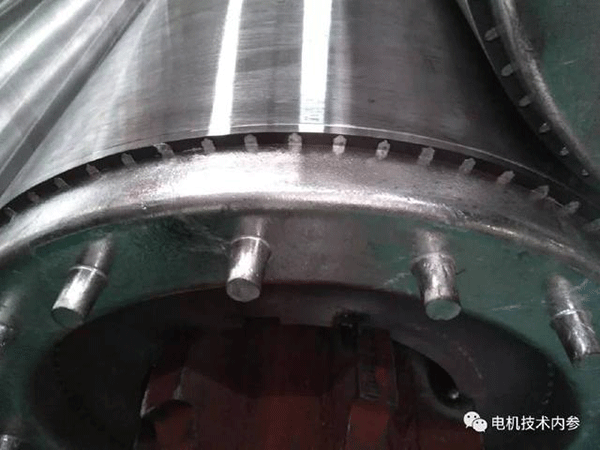
转子闭口槽详解
对于相同铸铝工艺的电机,半闭口槽和闭口槽设计是截然不同的设计思路。那么,转子闭口槽究竟是如何对电机各方面的性能产生影响的?怎样才能趋利避害提升电机效率?
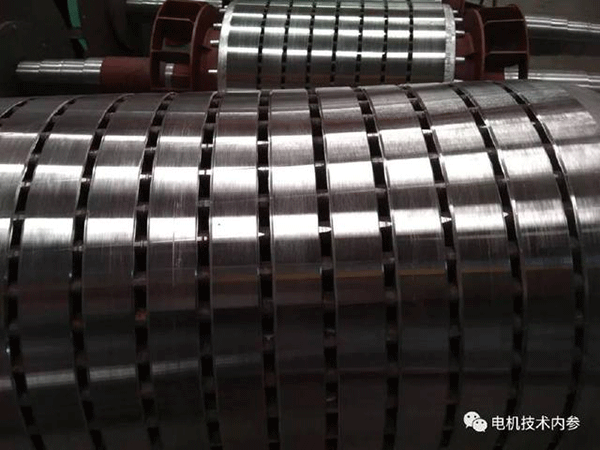
● 转子采用闭口槽虽可以减少电机的定子铜耗和杂散损耗,减少的幅度与闭口桥拱高度或磁桥厚呈正相关。
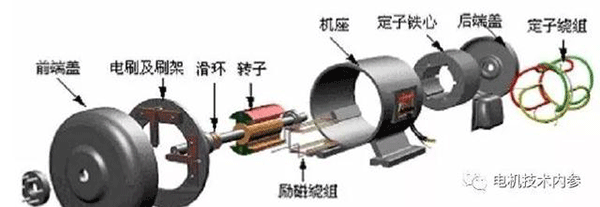
● 转子闭口槽磁桥厚过大,转子漏抗增大幅度变化较大,功率因数将趋于变差导致负载电流增加,使定转子铜耗、铝耗增加,抵消效率提升的成份甚至使效率反而下降。
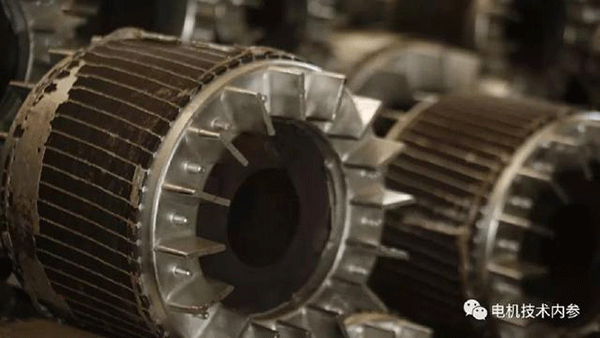
● 转子采用闭口槽,因漏抗增大使起动电流有所下降,但同时起动转矩、最大转矩也随之减小。因此,采用闭口槽时应同时兼顾起动和过载能力数据的变化不能低于标准允许的限值。
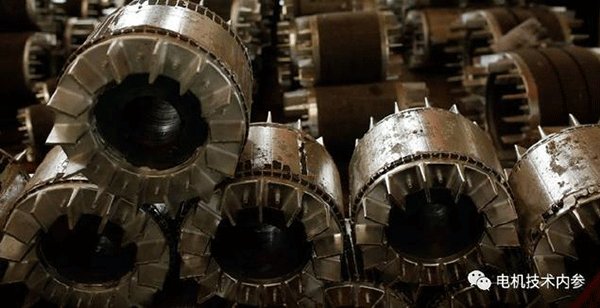
● 转子采用闭口槽后,噪声有一定程度的降低。尤其对电磁噪声和振动有极为明显的抑制作用。
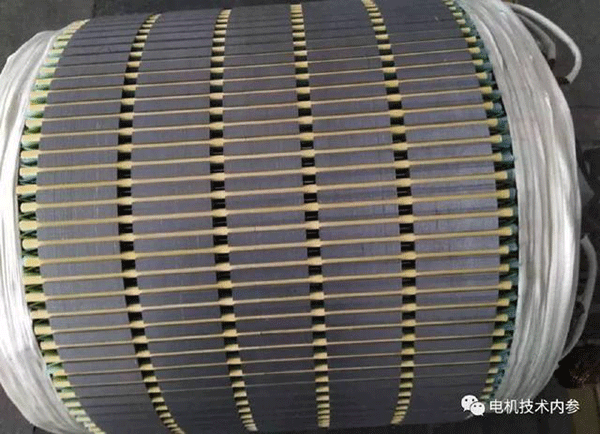
● 若能使闭口槽电机转差率维持半闭口槽的水平,效率提升的水平会更高。从各
电机厂家积累的一些具体试验数据看,桥拱高或磁桥厚为0.2mm左右的闭口槽效果较好。
#p#分页标题#e#
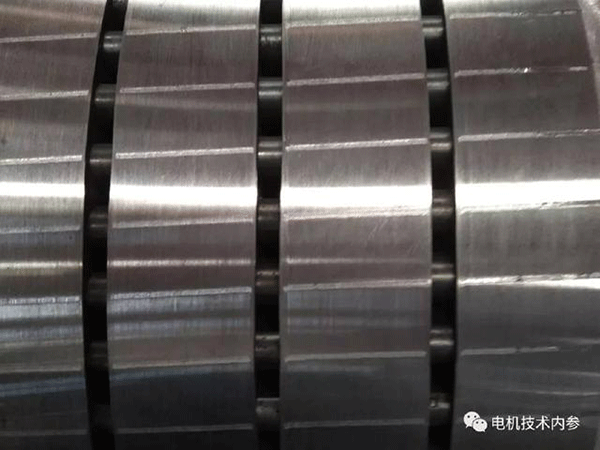
转子闭口槽加工工艺难度
与开口槽转子相比,在冲片冲制、叠压、铸铝过程都存在不同程度的难度,必须有足够的设备、工艺和工装保证。
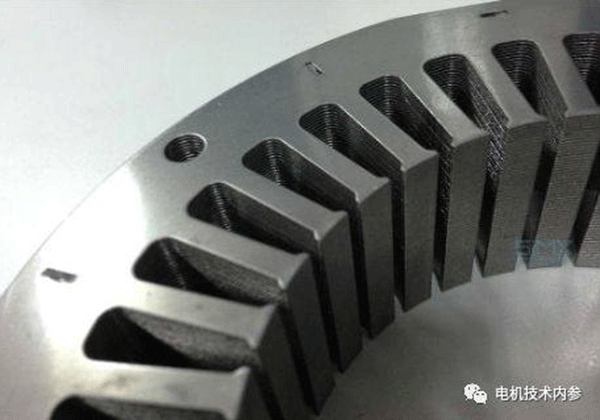
●冲片槽底与轴孔的同轴度不容易控制。冲片冲制时,定位必须精准,必须严格控制误差大小;
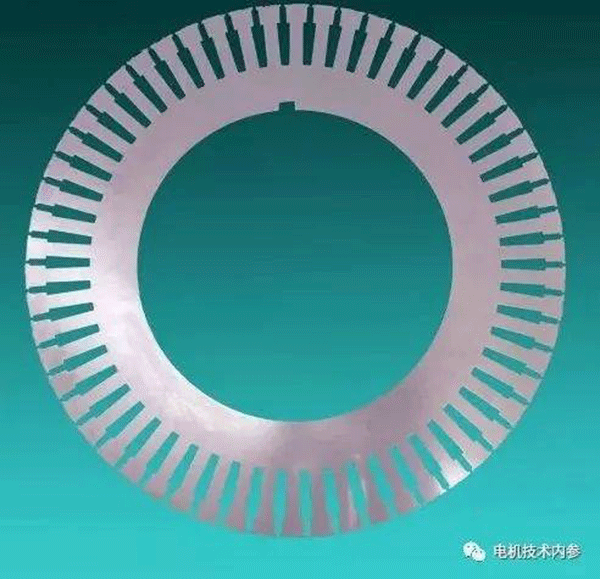
●转子叠压时因无槽口不可视,整齐度检查困难,易出现隐性锯齿问题,加大不可控因素。故而槽形棒尺寸精度和数量必须通过反复验证。
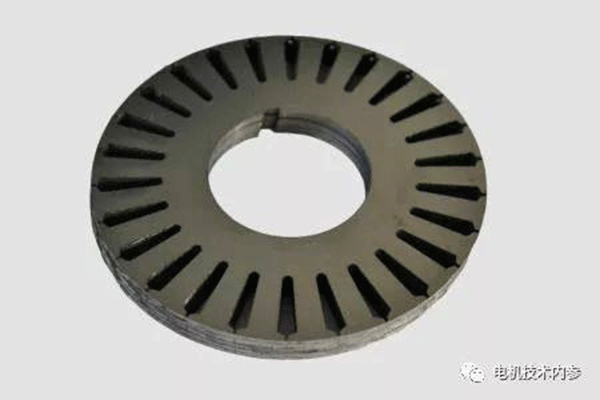
●铸铝过程中,特别是低压铸铝工艺,因排气问题易产生铸铝缺陷。应通过适度延长冷却时间,规避预防瘦条、端环部位缩孔的出现。
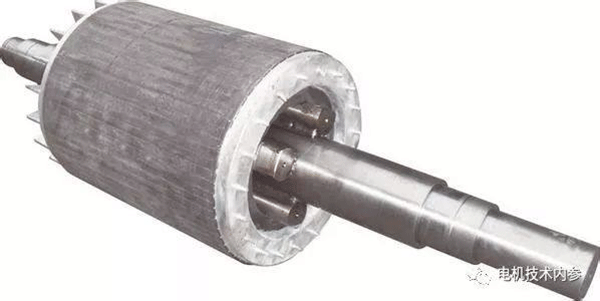
●铸铝过程的排气控制
一个效果非常不错的排气问题解决方案:在叠片时每隔一定的长度夹一张开口槽冲片,也就是在转子长度方向增加了多个排气面。注意开口槽冲片间隔长度与槽数及铁芯长度有直接关系,应通过试验不断修正。
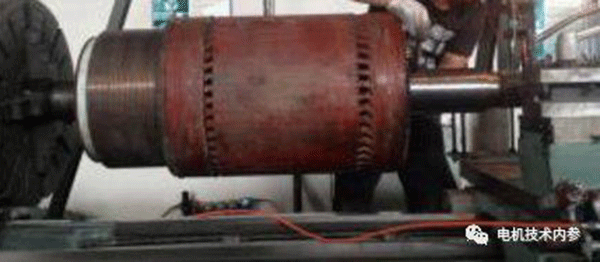
●转子车削也是一个非常关键的环节,可能因此导致截然不同的结果。因叠压和铸铝热变形引起的误差,各槽的磁桥厚度及其一致性极难保证,试验结果可能与设计预期相差较大甚至相反,除加强铁转子铁芯的叠压、铸铝过程控制外,应通过减小切削量或磨削方式的方式解决。
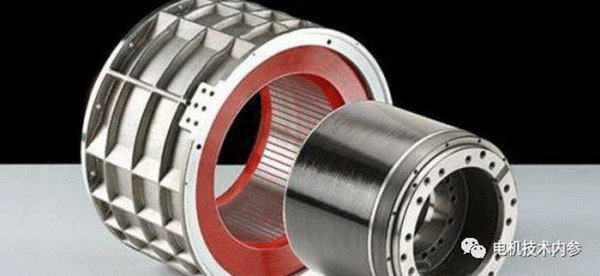
●闭口槽电机生产加工中具体问题。闭口槽电机提高本身效率的同时,对生产加工也影响巨大。如前述磨削工艺,效率低下的同时,还有磨削过程冷却液进入转子冲片的问题,因而必须增加转子加工后的烘干过程,以防止由此导致的对地故障。
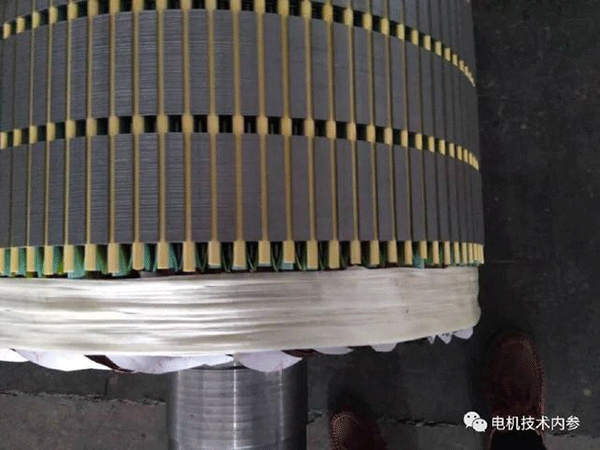
闭口槽铸铝转子前瞻性思考
#p#分页标题#e#
综上所述,我们可以发现追求电机性能的同时,生产加工效率和生产成本也是一个不可回避的问题。然而正是这些问题解决的现实需求,才使创新和进步拥有了不竭动力。
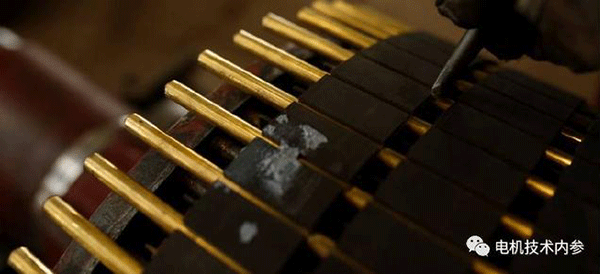
核心关键词:
西玛电机
西安西玛电机
高压电机
低压电机
西安电机厂
直流电机
交流电机
变频电机
防爆电机
电机控制柜
电机设计制造
电机配件
电机维修
来源网址:
https://www.simo.org.cn/zhengcefagui/3449.html